|
Pretreatment is important for spray quality
control - no grease, no rust and no
scratches on objects
Objects with
pretreatment can have
1.
greater paint
adhesion
2. higher
paint corrosion-resistance
3. greater
chemical resistance
|
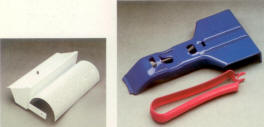 |
Pretreatment
methods
-------------------------------------------------------------------------
Plastics |
|
Annealing
Plastics is easy to transform during curing, so
pre-heating plastics to its pre-transformation stage
is required to reduce its internal stress
Organic solvent degreasing
Benzene, xylene, trichloroethylene is used for
degreasing. Rinsing afterwards is necessary to
reduce oil film deposited during degreasing
De-ionizing
Plastics is a bad conductor which is easy to attract
electrostatics, de-ionizing gun is necessary to
remove electrostatics after pretreatment
Surface improvement
to make plastics surface be
coarser and more chemical resistant for better paint
adhesion by:
1. sand blasting
2. UV curing
3. flame oxidation
4. solvent etching
Drying
Drying is necessary for
corrosion resistance after pretreatment
|
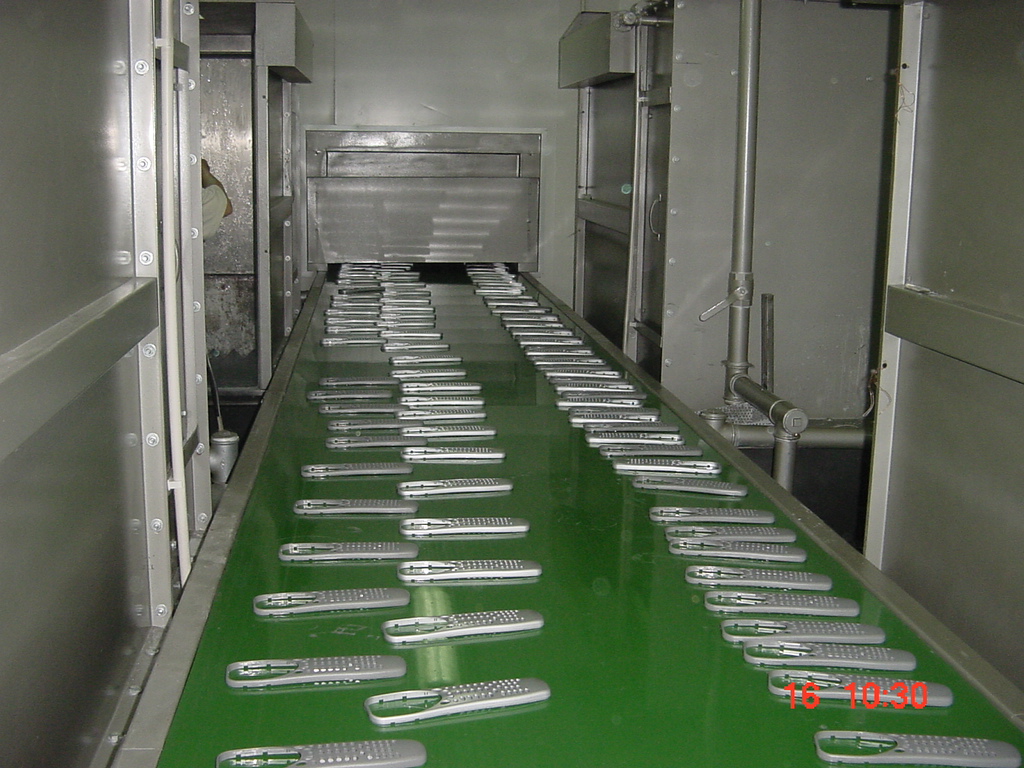 |
 |
Steel |
|
Degreasing:
1. Organic solvent degreasing
Benzene, xylene, trichloroethylene is used for
degreasing. Rinsing is necessary afterwards to
reduce oil film deposited during degreasing
2.
Alkaline degreasing
to remove animal or plant oil
by the action of alkaline solution and saponifiable
oil
surfactant/Emulsifier is
required to remove
saponifiable oil (lubricant, anti-rust paint) as
alkaline solution is
not effective to remove sponifiable oil
3. Ultrasoun d degreasing
to clean object surface by
impact wave of ultrasound
is suitable for objects with
difficult edges (e.g. eye frames)
Derusting
1.
mechanical derusting/sand blasting
use sand particles to derust steel by centrifugal
action of sands
2. acidic derusting
use hydrochloric acid, sulfuric
acid, nitric acid or hydrofluoric acid to remove
rust and oxides on objects. Etching relieving agent
is recommended to avoid over-etching.
Deoxidizing
is
required before phosphating to avoid over-etching
during acidic derusting
Phosphating
to
improve paint adhesion & corrosion resistance by
creating a conversion coating on the object
Phosphating can be divided into
1.
Iron
phosphating
use
ferric salt phosphates to make a thin phosphate
coating on iron, low phosphating temperature is
required
suitable for objects with high exterior requirement
but
low corrosion resistance (e.g. electro-plating,
electrostatic painting)
2.
Zinc
phosphating
use
zinc salt phosphates to make a thick phosphate
coating on iron, high phosphating temperature is
required
suitable for objects of low exterior requirement but
high corrosion resistance (e.g. derusting objects,
stretching objects)
Drying
Drying is necessary for
corrosion resistance after phosphating
|
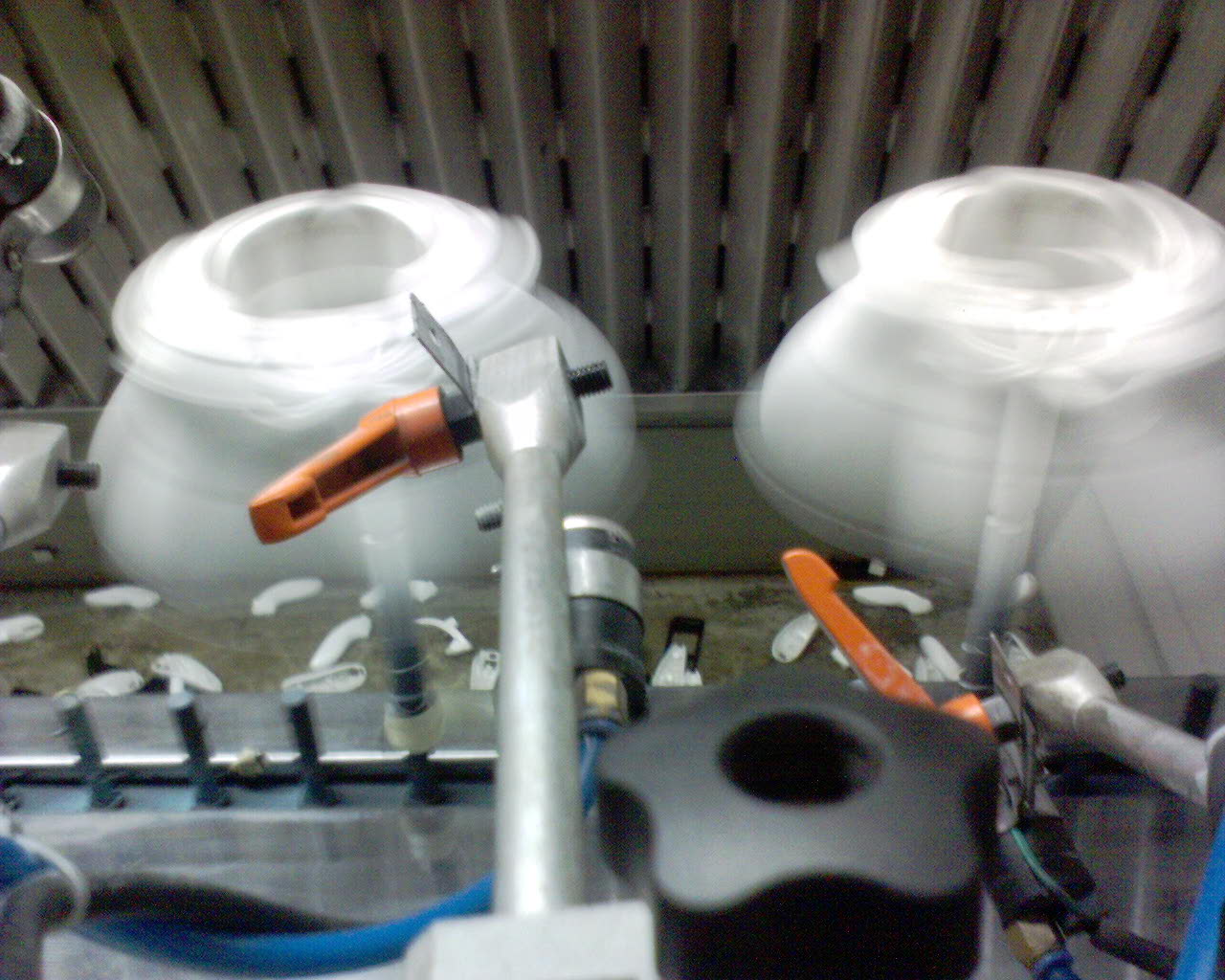 |
 |
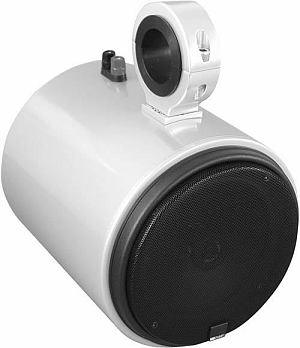
|
|
Aluminum alloy |
|
Degreasing:
1. Organic solvent degreasing
Benzene, xylene, trichloroethylene is used for
degreasing. Rinsing is necessary afterwards to
reduce the oil film deposited during degreasing
2.
Alkaline degreasing
to remove animal or plant oil
by the action of alkaline solution and saponifiable
oil
surfactant/Emulsifier is
required to remove
saponifiable oil (lubricant, anti-rust paint) as
alkaline solution is
not effective to remove sponifiable oil
3. Ultrasoun d degreasing
to clean object surface by
impact wave of ultrasound
is suitable for objects with
hard to reach edges (e.g. eye frames)
Deoxidizing
is
required before phosphating to avoid over-etching
during acidic derusting
Drying
Drying is necessary for
corrosion resistance after phosphating or cleansing
|
 |
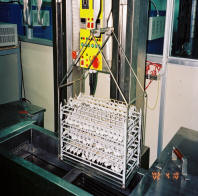 |
Choosing your pretreatment line
-------------------------------------------------------------------------
Spraying Pretreatment Line |
|
1. cleaning method
to pump
out cleansing detergent by spray nozzles
2.
Suitable for
alkaline
cleansing, surfactant cleansing
3.
Advantages
degreasing
temperature can be lowered to below
50℃
and faster degreasing time
4. Disadvantages
only
suitable for simple objects, not
suitable for objects with difficult edges
|
Immersion Pretreatment Line |
|
1. Immersion tank
a. 2
types of immersion tanks
i. 'ship'
tank: overhead conveyors to put objects into immersion tanks
ii.
rectangular tank: reciprocators
or chain hoists to put objects into immersion tanks
b.
made of
i.
degreasing tank: steel
ii.
derusting tank: fibre reinforced plastics or stainless steel
iii.
phosphating tank: stainless steel with insulation layer to
reduce heat loss
c.
heating elements
i. direct
heating: boil water with heating elements
ii. indirect
heating: heat up tank water with heat exchangers, suitable
for phosphating tank to reduce heat transfer loss if
phosphates are deposited in tank
2.
Suitable for
Alkaline
cleansing, surfactant cleansing or ultrasound cleansing
3.
Advantages
can
cleanse complex or objects with difficult to reach edges
4.
Disadvantages
need to
boil water up to 60℃
with agitation
larger workshop
longer pretreatment time
|
DRYING OVEN
-------------------------------------------------------------------------
|
Drying is
necessary for corrosion resistance after phosphating
or cleansing
Drying time is
important for corrosion resistance
|
|